You are here: Home > News > Company News > Effect of Temperature on Molding of Aluminum Alloy Die Casting Mould
Plastic Parts
Effect of Temperature on Molding of Aluminum Alloy Die Casting Mould
There are many factors that affect the quality of aluminum alloy die casting. For example, the type and quality of the die casting machine. In general, an increase in the temperature of the aluminum alloy die-casting mold lowers the condensation layer of the plastic in the cavity in the morning, making it easier for the molten material to flow in the cavity, thereby obtaining greater part weight and better surface quality. The fairness of the geometry and technical requirements of die castings. The mold structure is the same as the operator's process water. At the same time, the increase in mold temperature will also increase the tensile strength of the part.If the aluminum alloy die-casting parts and the mold parts are complicated, the processing of the aluminum alloy die-casting parts will be difficult and the precision is not high. The aluminum alloy die-casting forging process is a special die-casting die-finishing machine. The basic process is to first fill the liquid zinc alloy die-cast metal into the cavity of the mold at a low speed or high speed. The mold has a movable cavity surface. Due to the cooling process of the liquid metal, it is forged under pressure, which not only eliminates the shrinkage defects of the blank, but also makes the internal structure of the blank reach the forged broken particles. If the aluminum alloy die-casting parts are combined, the machining process is greatly simplified, and high machining precision is easily obtained, thereby obtaining high-quality aluminum alloy die-casting parts. Therefore, it is necessary to isolate the mold from the machine plate and mold surface (if possible). If hot runner molds are considered, heat exchange between the hot runner parts and the cooled spray parts is minimized. This method can reduce energy loss and warm-up time.
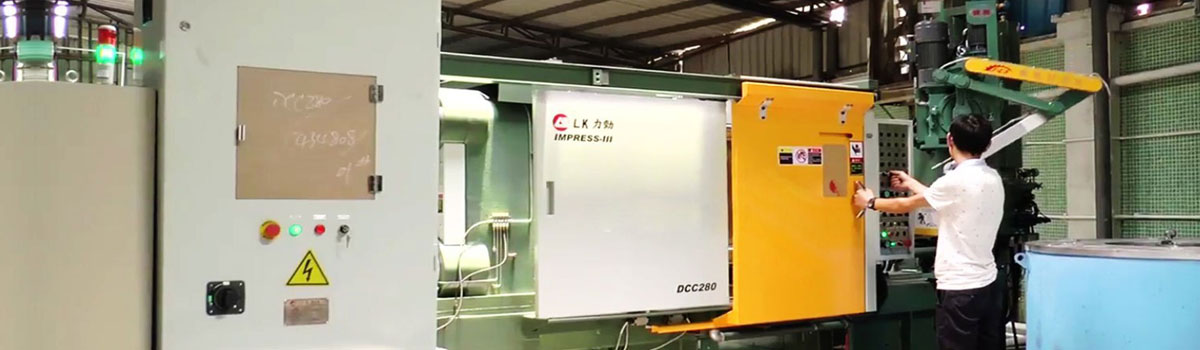
The number of die-casting cavities of aluminum alloy determines the number of die-casting cavities of aluminum alloys. It is necessary to consider the equipment capacity, and the processing of aluminum alloy die-casting molds is difficult. Temperature control has an important influence on the purpose of formability, the appearance of materials, physical properties, and molding cycle. In general, keeping the core temperature at a lower level can increase the injection time. However, the molding cycle associated with the shape of the product and the type of finished material also depends on the temperature at which the core is filled. Production batch size, casting precision requirements, etc., especially for multi-cavity molds, because the aluminum alloy die-casting mold is difficult to process, the dimensional accuracy error is large, the channel structure is not easy to achieve balance, and the performance of each cavity casting is not the same. Aluminum alloy die castings have high precision requirements. When the geometry is complex, it is best to make it one cavity. Small castings are subject to availability.
Contact us:
Web: www.tmetalparts.com
Email: sales@tmetalparts.com
Call: (0086) 13688956239
Wechat: (0086) 13688956239